In today’s interconnected global economy, the smooth flow of goods is critical to business success. Yet recent data suggests that supply chain disruptions lasting one month or more are expected to occur every 3.7 years, creating significant challenges for businesses worldwide. When freight delays occur, they don’t just affect a single shipment – they create ripple effects throughout the entire supply network, impacting production schedules, inventory levels, and ultimately, the bottom line.
This guide examines how freight delays impact supply chains and provides practical strategies to avoid or mitigate these disruptions. Whether you’re a supply chain professional, logistics manager, or business owner, understanding these dynamics is essential for building resilience in today’s volatile shipping environment.
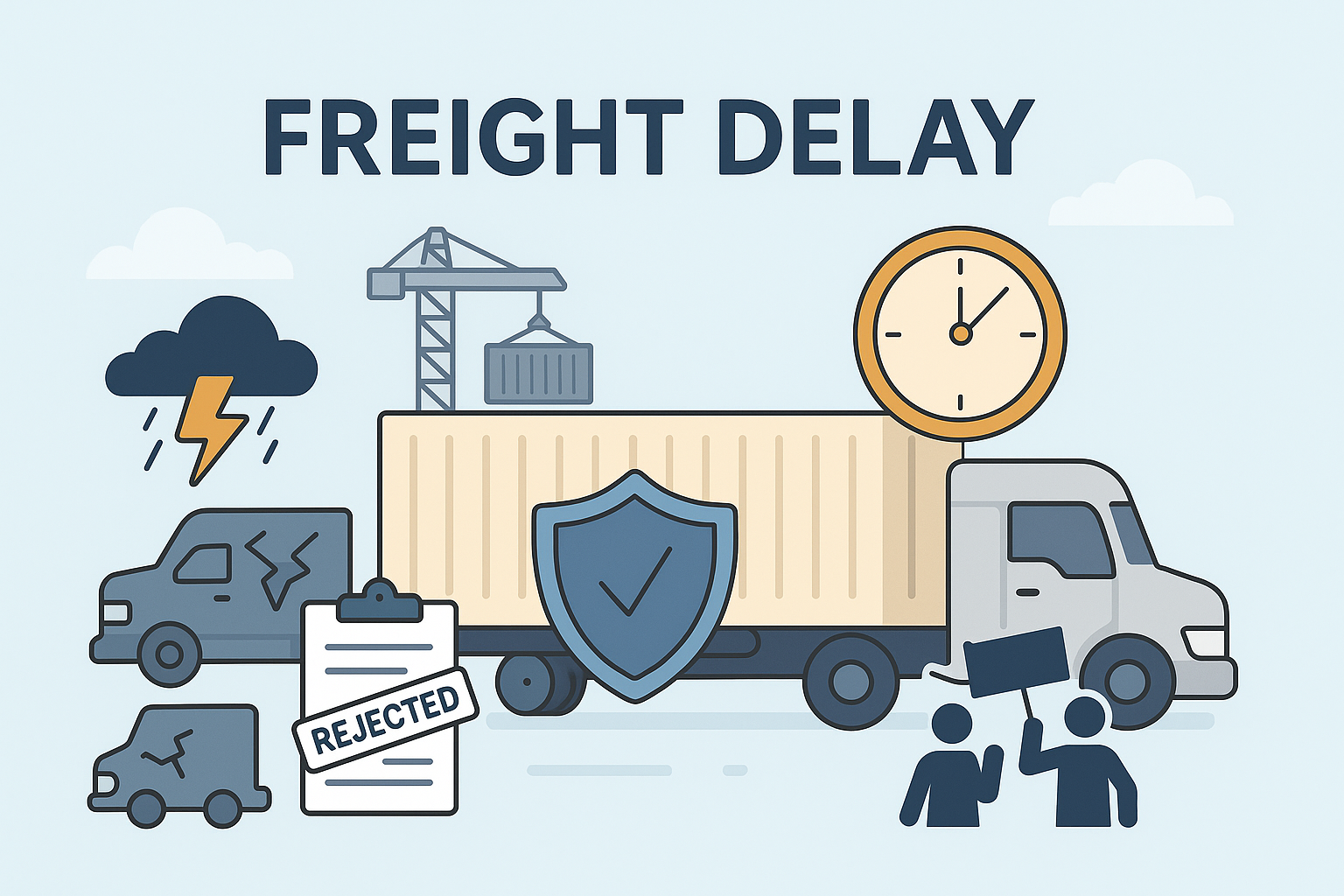
Understanding Freight Delays and Their Relationship to Supply Chains
What Are Freight Delays?
Freight delays occur when shipments fail to arrive at their intended destination within the expected timeframe. These delays can affect any mode of transportation – ocean, air, rail, or truck – and can range from minor setbacks of a few hours to major disruptions lasting weeks or months.
The Interconnected Nature of Modern Supply Chains
Modern supply chains function as complex, interconnected networks rather than simple linear processes. This interconnectivity means that freight delays in one area can quickly cascade throughout the entire system, creating what supply chain experts call the “bullwhip effect.”
When a shipment is delayed, the consequences extend far beyond the immediate transportation issue:
- Production lines may halt due to missing components
- Inventory levels fluctuate, creating stockouts or excess inventory
- Customer deliveries are postponed, affecting satisfaction and loyalty
- Cash flow is disrupted as goods remain in transit longer than anticipated
Research indicates that these cascading effects can amplify the initial disruption, with extended shipping times leading to production delays, increased inventory holding costs, and ultimately, material shortages causing line stoppages.
Common Causes of Freight Delays in Supply Chain
Understanding the root causes of freight delays is the first step toward developing effective mitigation strategies. These causes generally fall into three main categories:

Natural and Environmental Factors
Natural events represent some of the most unpredictable and impactful causes of freight delays:
- Extreme weather events like hurricanes, blizzards, and floods can shut down transportation networks for days or weeks
- Natural disasters such as earthquakes and tsunamis can destroy infrastructure and disrupt shipping routes
- Environmental conditions like drought can affect waterway levels, as seen in recent canal operations challenges
- Climate-related disruptions are becoming more frequent and severe, creating new challenges for supply chain planners
The recent drought affecting major shipping canals demonstrates how environmental factors can create global ripple effects, with additional operational costs ranging from $500-700 million for specific routes and extended transit times adding approximately two weeks to shipping schedules.
Operational Challenges
Day-to-day operational issues frequently cause freight delays:
- Physical roadblocks including construction, accidents, and infrastructure failures
- Equipment failures such as vessel breakdowns, truck malfunctions, or container shortages
- Documentation issues including customs delays, incomplete paperwork, or regulatory compliance problems
- Insufficient carrier capacity leading to overbooking and prioritization challenges
- Last-mile delivery complications in urban areas or remote locations
These operational challenges often compound each other, with documentation issues leading to customs delays, which then create capacity constraints as goods pile up at ports.
Systemic Issues
Broader systemic problems can create persistent freight delays:
- Labor shortages affecting ports, warehouses, and transportation providers
- Infrastructure limitations including aging ports, roads, and bridges
- Technological failures in tracking systems, communication networks, or logistics platforms
- Cybersecurity threats targeting transportation and logistics systems
These systemic issues often require long-term solutions and industry-wide cooperation to address effectively.
Economic Impact of Freight Delays
The financial consequences of freight delays extend throughout the supply chain, affecting businesses of all sizes and across all industries.
Direct Operational Costs
Freight delays create immediate financial impacts:
- Additional container and chassis requirements costing approximately $4 million annually per day of delay
- Increased inventory holding costs averaging $4 million weekly for major retailers
- Port disruption costs ranging from $65-150 million daily for major ports
These direct costs quickly accumulate, turning what might seem like a minor delay into a major financial burden.
Transportation Cost Increases
When freight delays occur, transportation costs typically rise as companies scramble to find alternative solutions:
- Truck transportation costs have increased by 13%
- Rail transportation costs have risen by 25%
- Air freight costs have grown by 11%
These increases reflect both the higher demand for alternative shipping methods and the premium prices carriers can command during disruptions.
Global Economic Impact
The ripple effects of freight delays extend throughout the global economy:
- Shipping rates on the Shanghai-South America route have reached $9,026 per TEU (twenty-foot equivalent unit)
- Rates on the Shanghai-South Africa route have nearly tripled to $5,426 per TEU
- Insurance premiums and fuel costs have increased significantly
These global impacts contribute to inflation and supply shortages, affecting consumers and businesses worldwide. Research projects a 0.6% increase in consumer prices by 2025 due to ongoing shipping challenges.
Strategies to Avoid or Mitigate Freight Delays
While freight delays cannot be eliminated entirely, businesses can implement various strategies to reduce their frequency and minimize their impact.
Supply Chain Restructuring
Fundamental changes to supply chain structure can significantly reduce vulnerability to freight delays:
- Nearshoring initiatives bring production closer to end markets, reducing transportation distances and complexity
- Supplier diversification prevents over-reliance on single sources that could become bottlenecks
- Creation of redundant supply networks provides alternatives when primary routes are disrupted
- Implementation of flexible logistics frameworks allows for quick adaptation when delays occur
Companies that have implemented these restructuring strategies report 35% fewer disruptions and 60% faster recovery times when delays do occur.
Technological Solutions
Modern technology offers powerful tools for managing and mitigating freight delays:
- Investment in visibility software provides real-time tracking and early warning of potential delays
- Implementation of predictive analytics helps forecast potential disruptions before they occur
- Real-time monitoring systems allow for immediate response when delays begin
- Enhanced inventory management systems optimize stock levels to buffer against delays
These technological solutions not only help manage delays when they occur but can often prevent them entirely by identifying potential problems before they escalate.
Operational Improvements
Practical operational changes can significantly reduce the risk and impact of freight delays:
- Proactive threat identification through regular risk assessments and scenario planning
- KPI monitoring to track performance and identify trends that might indicate future delays
- Continuity of Operation Planning (COOP) to ensure business can continue during disruptions
- Regular training and exercises to prepare teams for responding to delays effectively
Companies that implement these operational improvements report a 40% reduction in delay-related costs and a 30% improvement in on-time delivery performance.
Risk Management Framework
A comprehensive risk management approach provides structure for addressing freight delays:
- Development of comprehensive risk assessment protocols to identify potential vulnerabilities
- Implementation of hazard vulnerability assessments to prioritize the most critical risks
- Creation of alternative transportation strategies to provide options when primary methods are disrupted
- Establishment of crisis management protocols to guide response when delays occur
This structured approach ensures that freight delay management is integrated into broader business continuity planning rather than treated as an isolated logistics issue.
Future Considerations and Recommendations
As supply chains continue to evolve, several key areas will shape the future of freight delay management:
Technology Integration
The continued integration of advanced technologies will transform how businesses manage freight delays:
- Increased adoption of predictive analytics will allow for more proactive management
- Enhanced visibility solutions will provide greater transparency throughout the supply chain
- Automated documentation processes will reduce delays caused by paperwork issues
- Real-time tracking capabilities will enable more responsive decision-making
Businesses that invest in these technologies now will be better positioned to manage freight delays in the future.
Strategic Planning
Long-term strategic planning is essential for building resilience against freight delays:
- Development of comprehensive risk management frameworks that address all potential disruption sources
- Implementation of resilience measures that go beyond simple redundancy to include adaptability
- Creation of redundancy in critical areas without excessive cost or complexity
- Investment in infrastructure improvements that address systemic vulnerabilities
These strategic initiatives require executive-level commitment and cross-functional collaboration but provide significant long-term benefits.
Operational Excellence
Continuous improvement in day-to-day operations remains a critical component of freight delay management:
- Regular review and updating of procedures to incorporate lessons learned
- Continuous training and development to ensure teams can respond effectively to delays
- Enhancement of communication protocols to ensure all stakeholders are informed during disruptions
- Strengthening of partnerships and collaborations to create more resilient supply networks
This focus on operational excellence ensures that theoretical strategies translate into practical improvements in freight delay management.
Conclusion
Freight delays represent one of the most significant challenges facing modern supply chains. Their impact extends far beyond simple transportation issues, affecting production schedules, inventory levels, customer satisfaction, and ultimately, financial performance.
By understanding the causes and consequences of freight delays, businesses can implement effective strategies to avoid or mitigate them. From fundamental supply chain restructuring to technological solutions and operational improvements, these approaches can significantly reduce vulnerability to disruptions.
As global supply chains continue to face challenges from climate change, geopolitical tensions, and evolving consumer expectations, the ability to manage freight delays effectively will become an increasingly important competitive advantage. Businesses that invest in resilience now will be better positioned to thrive in an uncertain future.
The key to success lies not in eliminating freight delays entirely – an impossible goal in today’s complex world – but in building supply chains that can anticipate, adapt to, and recover quickly from the inevitable disruptions that will occur.